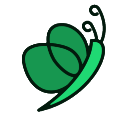
ΣEM : Track production processes in real time
ΣEM: in summary
In manufacturing and machining sectors, there is often a disconnect between what is quoted to the customer and what needs to be produced. Traditional management systems that focus on CRM and invoicing tend to overlook this gap. ΣEM addresses this issue by providing an integrated solution that unifies sales and manufacturing processes, offering real-time tracking and efficient resource management, making it a suitable tool for companies in these industries.
What are the main features of ΣEM?
Real-time Production Tracking
One of the key functionalities of ΣEM is its ability to track production processes in real time. This feature allows businesses to monitor every phase of an order, from the quoting stage through to delivery. The tool gives complete visibility into the status of each order, ensuring that all stages of production align with the initial quote and the customer's expectations.
- Continuous tracking from quote to delivery.
- Visibility into every stage of the production process.
- Real-time updates on order status.
Seamless CRM and Order Management Integration
ΣEM integrates smoothly with customer relationship management (CRM) systems and order management tools, helping to streamline business processes. This feature ensures that sales and production teams are in sync, reducing the risk of errors or miscommunications between the quoting process and the actual manufacturing work required. The integration of CRM tools also allows businesses to maintain better relationships with customers by improving order accuracy and response times.
- CRM and order management integration.
- Synchronization between sales and production processes.
- Simplified customer interaction and order handling.
Efficient Inventory and Resource Management
ΣEM also offers advanced features for managing inventory and resources. This capability is crucial for manufacturing businesses, where precise control over raw materials and human resources can impact production efficiency. With ΣEM, businesses can track inventory levels, manage work-in-progress, and allocate the right resources to each job, ensuring that projects stay on schedule and within budget.
- Inventory tracking for raw materials and work-in-progress.
- Resource allocation based on project requirements.
- Optimization of material and human resource usage.
Open Source and Community Collaboration
A defining aspect of ΣEM is that it is an open-source project. This allows users to access, modify, and contribute to the software’s development, fostering a collaborative approach to its continuous improvement. The open-source model ensures that the software evolves based on real-world feedback from businesses and developers, making it adaptable to changing industry needs.
- Open-source availability on GitHub.
- Contributions from a community of developers and users.
- Ongoing improvements based on collaborative development.
Modern Technology Stack
ΣEM is built using modern technologies such as Laravel 10, Livewire, and Bootstrap 4.6, which support the system’s scalability, performance, and user-friendly interface. These technologies allow for efficient handling of complex business processes while ensuring that the software remains responsive and accessible to users across various devices.
- Built on scalable and high-performance technologies.
- User-friendly interface for easy adoption.
- Adaptable to evolving business needs.
Conclusion
ΣEM is designed to close the gap between the quoting process and manufacturing operations, offering a cohesive tool for managing sales, production tracking, and resource allocation. By integrating CRM and order management, providing real-time production visibility, and leveraging open-source collaboration, ΣEM delivers a practical solution for machining and manufacturing businesses looking to streamline their processes.
ΣEM: its rates
standard
Rate
On demand
Clients alternatives to ΣEM

Streamline justice processes with this SaaS software. Automate tasks, manage cases, and track data to save time and increase efficiency.
See more details See less details
With this software, you can easily generate legal documents, communicate with clients, and access case information from anywhere. Customizable workflows and powerful reporting tools allow you to tailor the software to your specific needs.
Read our analysis about DiapazTo Diapaz product page
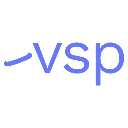
Streamline your business operations with our powerful ERP software. Manage your resources, track inventory, and improve productivity with ease.
See more details See less details
Our ERP software provides a centralized platform to manage all aspects of your business. From financials to procurement, inventory to production, VSPortage simplifies your operations and boosts efficiency. With real-time data insights, you can make informed decisions and drive growth.
Read our analysis about VSPortage (vsp)Benefits of VSPortage (vsp)
ERP 100% dedicated to umbrella companies
The most comprehensive functional coverage on the market
Easy to use
To VSPortage (vsp) product page
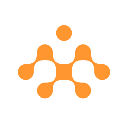
Streamline your business operations with an all-in-one ERP software. Manage inventory, finances, and customer relationships efficiently.
See more details See less details
Kafinea's ERP software provides a comprehensive solution for businesses of all sizes. Enjoy real-time reporting, customizable workflows, and automation to increase productivity and reduce errors. Stay on top of your business with Kafinea.
Read our analysis about KafineaBenefits of Kafinea
Unlimited users
Many automations and powerful workflows
Unlimited ERP features
To Kafinea product page
Appvizer Community Reviews (0) The reviews left on Appvizer are verified by our team to ensure the authenticity of their submitters.
Write a review No reviews, be the first to submit yours.